NIS machines increase efficiency
The Vetropack Group commissioned the first servo-driven NIS machine from Bucher Emhart Glass (BEG) at our Kyjov plant in the Czech Republic, at the end of 2023. This milestone not only highlights the long-standing collaboration between the two companies but also introduces a technological innovation with significant potential for the future for Vetropack. The NIS technology will further enhance production efficiency and reduce emissions at Vetropack's Croatian site in Hum na Sutli.
Vetropack and Bucher Emhart Glass (BEG) are taking their collaboration to a new level
Vetropack and Bucher Emhart Glass (BEG) have much in common: both companies have Swiss origins and are renowned names in the glass industry. They have enjoyed a successful partnership of over three decades, with each company’s expertise complementing the other’s. BEG is market leader in glass production technologies. It was nearly 100 years ago that the company, then known as Hartford-Empire, patented the Individual Section (‘IS’) machine, which enabled automated glass container production and set the industry standard, replacing competing technologies. Over the following decades, BEG continued to refine this solution. In the late 1990s, Emhart Glass joined Bucher Industries, marking a new chapter in their history.
“Over the years, we have built a strong partnership with BEG, based on mutual trust,” comments Martin Wakolbinger, Group Technology and Projects Manager in Technical Engineering at Vetropack. “Trust is very important in this industry. Naturally, BEG is not our only supplier. For each project, we compare offers from various suppliers. This was also the case when we planned to introduce the New Individual Section (NIS) technology at our Kyjov plant, for which we received proposals from four manufacturers. Ultimately, we chose BEG because they offered the most attractive overall package. Their technology impressed us the most, and communication with them is consistently open and responsive. BEG answers all our questions promptly.”
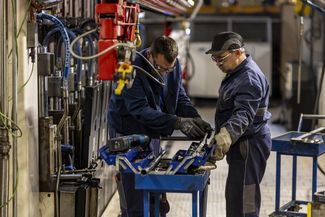
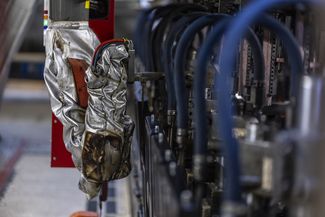
«To compete with the world's largest glass manufacturers, Vetropack relies on modern, highly efficient production technology. We provide customised solutions for each of its locations.»
The needs of these sites vary significantly, so the choice of technology depends on factors such as production series and runtimes. For instance, for the Boffalora site in Italy, BEG delivered six Advanced Individual Section (‘AIS’) machines in 2022. These machines allow Vetropack Italia to continue its tradition of producing intricate container designs in smaller production quantities, helping brands stand out in the market. “In Italy, flexibility is important. In Kyjov, on the other hand, we manage larger production series with longer runtimes,” explains Martin Wakolbinger.
Vetropack Moravia, a.s. in Kyjov is one of the largest glass producers in Central Europe. At the end of 2023, the site became the first within the Vetropack Group to commission a servo-driven glass production machine, the NIS machine. The goal was to achieve a higher production rate and significantly increase production efficiency – and this has been accomplished. “With the new NIS machine in Kyjov, we now produce three wine bottles per section instead of two,” says Martin Wakolbinger. “The investment in the NIS machine from BEG has fully met our expectations.”
NIS: highest-performing machine on the market
The NIS machine from BEG is regarded as one of the most flexible high-performance machines on the market today. It is distinguished not only by its high precision and efficiency but also by a significant reduction in energy consumption. Compared to traditional technologies, this provides a major advantage, improving Vetropack's environmental footprint.
The servo-electric forming technology of the NIS machine enables precise and repeatable movements, resulting in higher output and improved production quality. Another advantage of servo technology is its reliability independent of ambient temperatures – a key benefit when producing glass in challenging conditions. Product changes can be completed much more quickly, as the NIS with its range of different configurations accommodates a wide variety of container formats, making adjustments significantly simpler.
The reduced need for operator intervention compared to conventional pneumatic machines enhances operator safety. BEG has also developed optional safety features to protect operating personnel from accidental access to the pre-forming side during automatic operation. Additionally, the machine improves the working environment with a substantial reduction in noise levels.
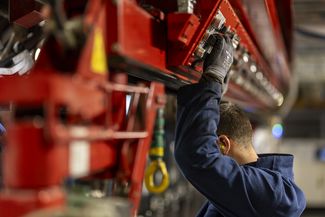
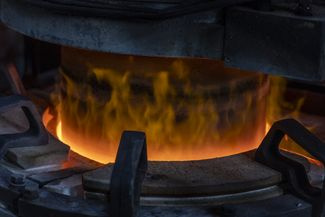
Continuous optimisation of technology
The NIS machine was first launched in 2000. Since then, BEG has continuously enhanced the technology. “The development of a glass production machine takes about 15 years to truly mature,” says Martin Wakolbinger. “We operate in a highly error-prone environment and don't have the capacity to implement ongoing technical optimisations ourselves. That's why we rely on equipment that has already been thoroughly tested.”
The implementation of the NIS machines in Kyjov was not without challenges, as the work took place during the Covid pandemic. Due to travel restrictions, conducting factory acceptance tests at BEG was difficult. “We addressed this digitally, carrying out the acceptance procedures via video conferencing, along with the exchange of extensive photo and video materials,” reports Michael Funkler. “Another hurdle during this period was the instability of global supply chains, which demanded a high degree of flexibility from everyone involved. However, thanks to our close cooperation, we successfully overcame these challenges,” Michael Funkler continues.
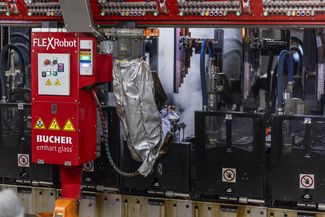
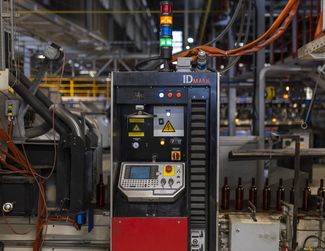
For Vetropack, the introduction of the NIS machine marked the beginning of a new era. “This is a completely new technical approach for us. Previously, we only used AIS machines in Kyjov, so we had to adapt all the moulds for the new machine. This was very time-consuming for everyone involved, but BEG provided excellent support,” says Martin Wakolbinger. In preparation for the project, BEG trained Vetropack's technicians on the new technology at its training centre in Sundsvall, Sweden, and explained the key differences between the new and existing machines.
Commissioning according to plan despite pandemic
In the end, the project in Kyjov went according to plan. “A few months after the start of production, our learning curve is still far from over, but the introduction of the NIS machine in Kyjov serves as a valuable example for other locations,” says Martin Wakolbinger. Following its successful deployment in Kyjov, the technology is now being installed at the Vetropack Straža d.d. site in Hum na Sutli, Croatia. There, too, the technology will make a significant contribution to improving energy efficiency and minimising the CO2 footprint. This marks another important step in the continuous modernisation and optimisation of glass production within the Vetropack Group.
The introduction of the NIS machines in Kyjov and Hum na Sutli also exemplifies the successful collaboration between two leading companies in the glass industry. With this technology, Vetropack has ushered in a new era of glass production, increasing both efficiency and quality of production while significantly reducing energy consumption and operating costs. “With the new technology, we have elevated our long-standing partnership with Bucher Emhart Glass to a new level. To maintain Vetropack's competitiveness in an increasingly demanding market environment, our cooperation with BEG will continue to play an important role in the future.”
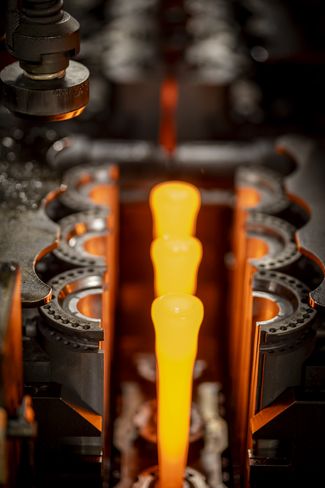